Nothing beats a cover story!
We feature on the front cover of the October edition of the International Design Engineer.
This article highlights how 3D printing is enabling Clogworks to design and manufacture customisable, lighter and more durable components when compared to traditional methods.
“We wanted to be able to create the CAD (designs), do all the research and development and create a high-end product almost entirely in-house and over the years, we’ve gained the people and equipment that allow us to make even better products. 3D printing is something I looked at many years ago, and now it’s an integral part of our product development." - Peter Opdam.
This technology not only allows to keep all of our research and manufacturing in-house, but it also enables us to rapidly design and manufacture components to help tailor our platform to our customers' exact requirements.
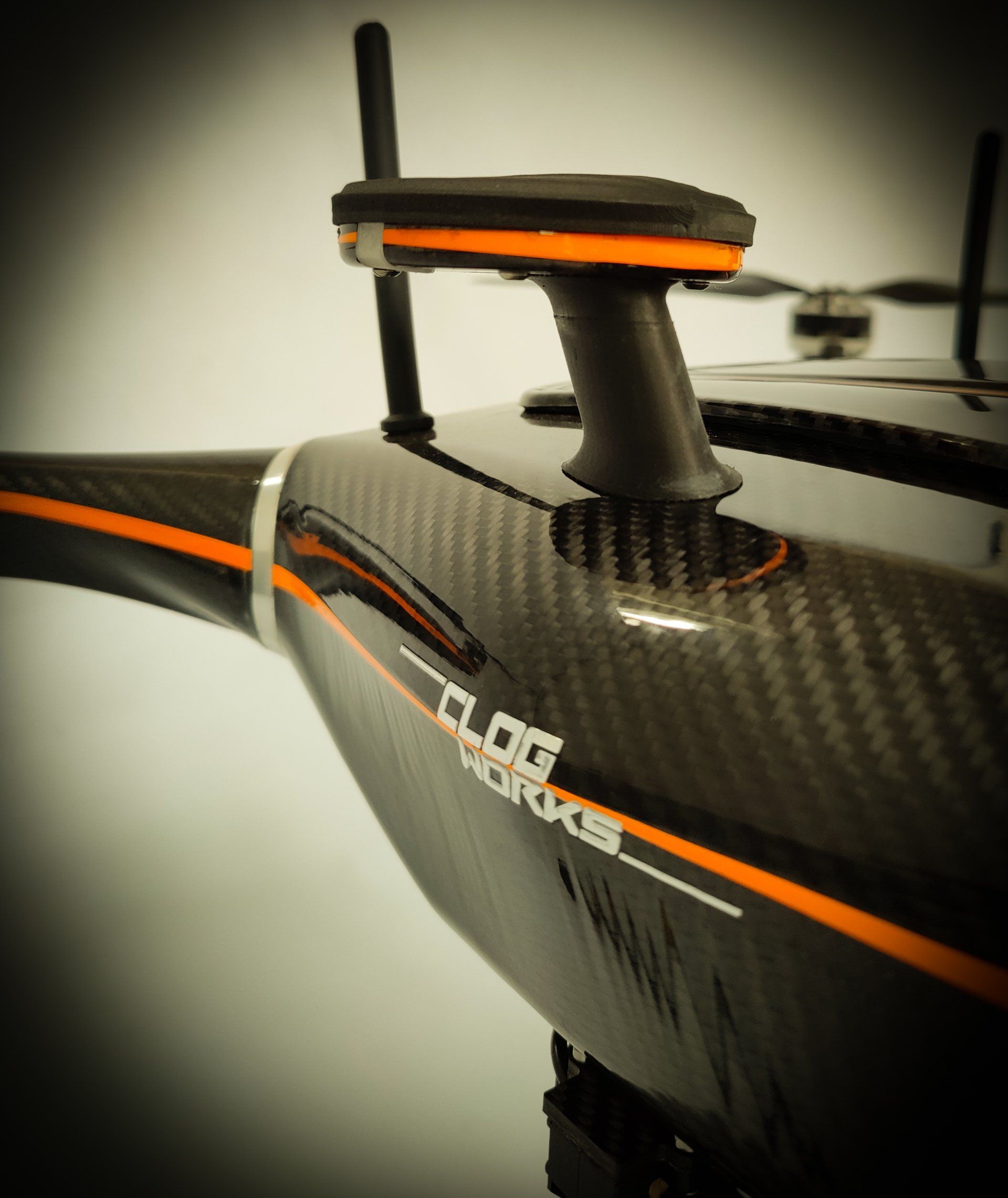
Dark Matter - Modular from the ground up
Our ability to customise virtually any component of our aircraft puts us in a unique position as a manufacturer.
Our completely modular airframe creates maximum flexibility, enabling our customers to effortlessly switch between components for more payload clearance and drivetrain options. This is then further complimented by our capacity to create custom 3D printed parts to build solutions to meet even the most specific customer requirements.